1. Principales características de la leche en polvo
Tanto si procede de leche entera, desnatada o semidesnatada, la leche en polvo es la forma de leche más fabricada y la más presente en la industria alimentaria mundial. En efecto, tanto si esta leche procede de vacas como de cabras, como ocurre en algunas regiones del mundo, la leche en polvo ofrece verdaderas ventajas, en particular su calidad conservadora.
La leche en polvo, antes conocida como harina de leche, se elabora a partir de leche deshidratada. Puede endulzarse (adición de glucosa) o implementarse con diversos aditivos como vitaminas, minerales o aminoácidos.
La leche se compone de aproximadamente un 87,5% de agua. Su deshidratación por evaporación y posterior secado reduce esta tasa al 3%. La leche en polvo tiene así la ventaja de conservar todas las proteínas, sales minerales y grasas de la leche (si no está desnatada) con un contenido reducido de agua que permite su conservación durante largos periodos de hasta un mes. Sin embargo, su creación requiere la puesta en marcha de infraestructuras y procesos que acaparan recursos, conocimientos y experiencia técnica.
2. Principales ámbitos de aplicación de la leche en polvo
La leche en polvo se utiliza en la producción de muchos productos industriales, especialmente productos lácteos como quesos, yogures y, por supuesto, leche en polvo para bebés.
Además, la leche en polvo también es utilizada por los particulares, que pueden emplearla en la elaboración de platos como tortitas, pasteles, postres lácteos o todo tipo de productos de pastelería. Por último, puede ser simplemente almacenado para su uso posterior o puramente especulativo.
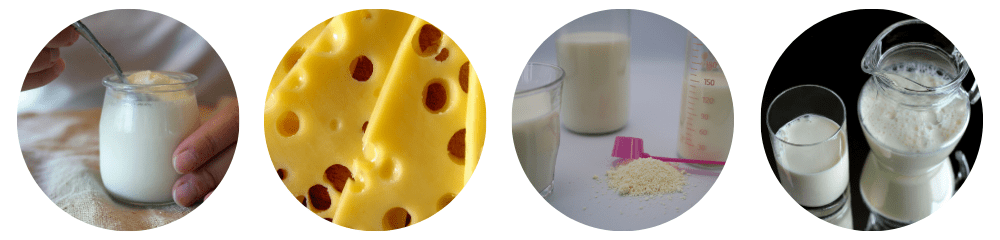
3. Manipulación industrial de la leche en polvo
Procesos e infraestructuras que intervienen en la creación de la leche en polvo
Antes de la pasteurización, la leche cruda se analiza varias veces para comprobar que cumple las normas establecidas por los organismos de control y se normaliza. Primero se separa la leche y la nata, luego se ajusta el nivel de grasa del producto (grasa que, recordemos, estará presente en cantidades iguales en la leche en polvo obtenida al final) y, por último, se añade más o menos nata en función del producto final deseado. Esta leche estandarizada se pasteuriza a continuación. Se somete a un tratamiento térmico a temperaturas en torno a los 72 °C para eliminar los microorganismos patógenos para el ser humano.
En esta fase, la leche puede consumirse en el plazo de una semana y puede comenzar el proceso de transformación en polvo. A continuación, se concentra la leche líquida. Esta concentración, realizada generalmente al vacío, consiste en una transferencia de materia (paso del agua de la leche al estado de vapor dejando un líquido residual más concentrado) y en una transferencia de calor (calor sensible para calentar la leche y calor latente para la evaporación y condensación del agua). Reduce el nivel de agua presente en la leche y la prepara para la siguiente fase de secado.
Por lo tanto, la fase de secado sigue a la fase de evaporación. En el caso de la leche en polvo, el secado puede llevarse a cabo de dos maneras diferentes. La elección de uno u otro depende, obviamente, de las características del producto inicial, pero sobre todo de la forma deseada del producto final.
El primer método posible es el secado por aspersión. Es la técnica más utilizada en la industria láctea y consiste en secar por aspersión el producto a secar (en forma líquida o en suspensión) en una corriente de gas caliente (nitrógeno o aire). El líquido se pulveriza en finas gotas en una torre de secado (torre de pulverización) en contacto con una corriente de aire caliente para evaporar el agua. El polvo obtenido es transportado por el flujo de calor a los ciclones (generalmente en número de dos: uno estático y otro dinámico) que separarán el aire del polvo con un rendimiento de unas 3t/hora. El segundo método es el de los cilindros calentados (o proceso Roller). Este último es un proceso de secado por ebullición. Consiste en utilizar el calor latente de vaporización para calentar el producto por conducción desde una superficie calentada por el vapor de agua (en este caso la superficie de dos cilindros giratorios con ejes horizontales). El producto en forma líquida se vierte entre los dos cilindros. En los rodillos se forma una fina capa que, tras secarse, puede eliminarse con una herramienta de raspado. El vapor de agua se elimina por aspiración con la ayuda de una campana situada encima de los cilindros.
En todos los casos, la leche está en forma de polvo al final del proceso de secado. A continuación, sólo queda tamizar y envasar el producto de salida en la forma adecuada al sector de actividad del cliente: Big Bag para la industria, saco de 20kg por ejemplo para profesionales o envases más pequeños para particulares.
4. Aplicaciones de la leche en polvo con los equipos de Palamatic Process
Una consulta con un especialista de Palamatic le ayudará a desarrollar un proceso de envasado en big bag en una zona higiénica (conocida como "zona blanca") para su leche en polvo. Este proceso consta de tres puntos que acompañan al polvo desde su creación, pasando por la fase de secado, hasta su ensacado.
Primer punto: sala limpia de envases
El objetivo de la instalación es diseñar una unidad de envasado que permita poner la leche en polvo en big bags y sacos en la misma estación sin riesgo de contaminación cruzada y externa.
La estación de llenado de sacos y big bags está instalada en una sala limpia totalmente de acero inoxidable que garantiza la higiene y la limpieza de los envases a la salida de la sala de producción. Un conjunto de SAS con gestión de la sobrepresión garantiza un aire y una atmósfera ultralimpios en las zonas de envasado. La sala de envasado diseñada y fabricada íntegramente por Palamatic Process es de acero inoxidable 304. Todos los equipos de acondicionamiento están "suspendidos" de la estructura de la sala para que no haya elementos en el suelo. Este diseño único ofrece una fácil limpieza.
Sobre la estación de llenado de big bags y sacos, en el exterior de la sala blanca, hay un depósito de acero inoxidable. Esta tolva pulmón de diseño fácil de limpiar está equipada con una válvula de alimentación de producto y tiene una capacidad de 3.000 litros. Se controla a través del PLC. La tolva está equipada con un fondo retráctil que permite la inspección por parte del operador. La tolva tiene un diámetro de 800 mm y permite un acceso ergonómico al operario. Se articula directamente sobre los pies de la tolva. Este acceso facilita las inspecciones de los operarios después de las fases de limpieza in situ (CIP) garantizando los controles de higiene.
Un muestreador de tornillo extraíble automático garantiza el muestreo regular y automático de todos los lotes de producción.
Segundo punto: llenar las bolsas grandes
El operador accede al manguito de big bag a través de una plataforma y coloca el manguito de big bag en la articulación inflable.
A continuación, controla las diferentes fases de llenado del big bag a través del panel de control: el arranque y la parada del ventilador durante un tiempo de retardo fijo, el control de las válvulas de apertura de las redes de desempolvado e inflado del big bag, así como la autorización de la apertura de la válvula de suministro de producto. La bolsa grande está preinflada por un ventilador equipado con filtros H7 G4 para un aire perfectamente limpio.
Los sensores de compresión (células de carga) informan al PLC del nivel de llenado del big bag y, una vez alcanzado el peso establecido (pesaje comercial), la válvula se cierra. Al final de la dosificación, el sello de inflado se libera para permitir la evacuación de la bolsa grande.
Tercer punto: llenar las bolsas
Para garantizar el envasado en bolsas, un tubo de caída del producto de acero inoxidable 316L permite alimentar la válvula de dosificación específica. Este sistema permite al usuario anular todas las restricciones dimensionales de las "aberturas" de la bolsa. En efecto, el sistema de sellado y anillo de presión permite envasar cualquier tipo de bolsa gracias a este sistema de pellizco.
Un modo de bolsa está integrado en el PLC para garantizar el control del operador. La estación de llenado de bolsas Palsack® está equipada con una plataforma de pesaje. Una campana de aspiración permite eliminar eficazmente el polvo durante las fases de desgasificación de las bolsas. La paletización de las bolsas soldadas y cosidas la realiza el operario mediante un manipulador de sacos al vacío.
5. Aplicaciones de clientes de Palamatic Process con leche en polvo
Desde 1992, Palamatic Process ayuda a las fábricas de leche -principalmente de la industria láctea y de la alimentación infantil- en su producción cumpliendo las estrictas normas, sobre todo de higiene, a las que están sometidas. Ya se han puesto en marcha algunas instalaciones que demuestran su eficacia:
- Una línea de molienda de leche en polvo
- Un proceso de mezcla de ingredientes para fórmulas infantiles que consiste principalmente en un equipo higiénico fácilmente desmontable.
- Patín de preparación y envasado de leche en polvo para lactantes
Para descubrir todas las aplicaciones realizadas en nuestros clientes, consulte nuestros estudios de casos en las industrias láctea y de alimentación infantil.