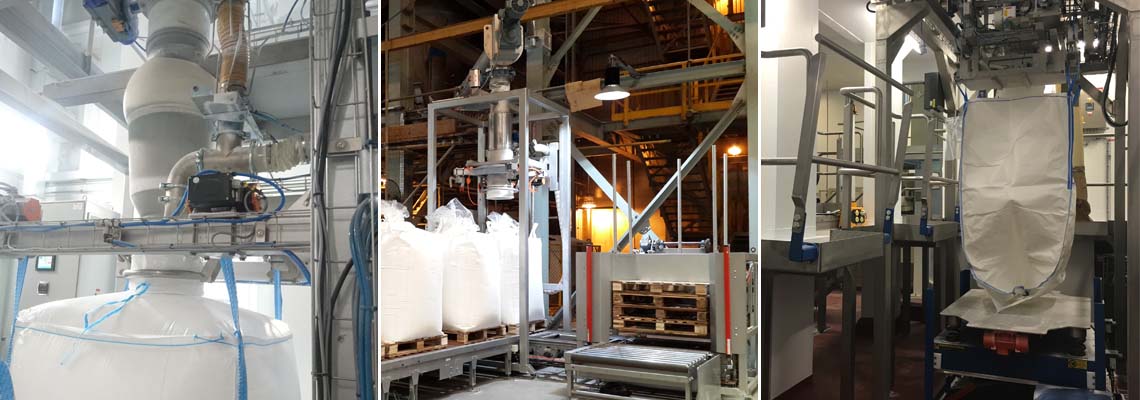
En la mayoría de las aplicaciones industriales, hay dos razones principales por las que una planta invierte en una estación de llenado de súper sacos automatizada:
- Minimizar la intervención del operador
- Para cumplir los objetivos de aumento de la demanda/rendimiento de los productos
¿Cuáles son los diferentes equipos para la implantación de un sistema de llenado de súper sacos de alta velocidad?
1. Tolva de pesaje
Las tolvas tampón pesadas que alimentan las máquinas de envasado de súper sacos son uno de los componentes más importantes de los sistemas de alto rendimiento. Estos depósitos de polvo se utilizan para almacenar temporalmente polvos y gránulos para garantizar una alimentación precisa y controlada del proceso de producción.
Los componentes más comunes utilizados en las tolvas de pesaje son las sondas de nivel alto, las sondas de nivel bajo y las células de carga (también llamadas células de carga). Las sondas de nivel sirven para indicar el nivel de llenado de la tolva a los equipos anteriores y activar así el llenado o vaciado de la misma.
Para obtener automáticamente un peso de llenado preciso en los súper sacos posteriores, se instalan células de carga bajo los soportes de la tolva. Estas células de carga se utilizan normalmente en sistemas que utilizan la función de "aumento de peso" o "pérdida de peso".
Las células de carga indican al sistema de control que se ha alcanzado el peso objetivo de polvo en la tolva. Cuando se trata de un sistema automático de llenado de súper sacos que requiere altas tasas de empaquetado de súper sacos, las tolvas de acumulación de doble peso funcionarán secuencialmente.
Cuando las tolvas de acumulación de peso están instaladas muy cerca unas de otras y alimentan la misma estación de llenado de súper sacos, la primera tolva que contiene el polvo puede descargar en el súper saco mientras la segunda tolva se está llenando. Al trabajar de esta manera en tiempo enmascarado, siempre hay una tolva llena lista para llenar un súper saco.
Las tolvas tampón pesadas suelen estar dimensionadas en función de la densidad aparente del polvo que se manipula y de la capacidad del súper saco que se va a llenar. En la salida de la tolva se instalan válvulas de mariposa o de compuerta para controlar el flujo de polvo.
Otros componentes pueden completar la instalación. De hecho, los dispositivos de ayuda al flujo, como los motores vibratorios, las boquillas de chorro de aire, los martillos neumáticos, etc., ayudan a evitar los problemas de aglomeración o puenteo cuando se trata de polvos que tienden a fluir mal.
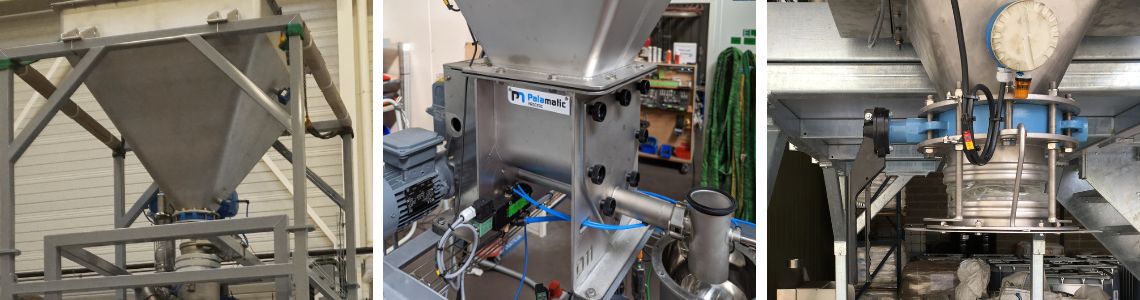
2. Equipos de control de flujo y dosificación de polvo
Otro elemento clave para conseguir altos índices de llenado de súper sacos es la forma de manipular y dosificar el polvo una vez que sale de la tolva de alimentación.
Como se ha mencionado anteriormente, se suele utilizar una válvula de mariposa o de cuchilla como válvula principal para controlar el flujo de polvo que sale de la tolva.
Desde este punto, mientras el polvo fluye a través de una rampa de alimentación por gravedad hacia la estación de llenado situada más abajo, puede dirigirse a uno de los dos conductos.
El conducto principal es el de alto caudal. A menudo se complementa con válvulas de mariposa justo por encima y por debajo de los canales.
Cuando el big bag se llena hasta el 95% de su capacidad total, la válvula de mariposa situada en la parte superior del conducto de alto caudal se cierra y desvía el polvo al alimentador de tornillo. El alimentador de tornillo proporciona una precisión repetible en la dosificación de polvo. Consta de una tolva integrada con un agitador que alimenta un tubo. En el interior del tubo hay un pequeño tornillo que empuja el producto hacia el extremo de salida en dirección al proceso posterior. Estos alimentadores de tornillo ofrecen una buena precisión de dosificación de hasta -/+ 1-2 gramos.
Otro tipo de sistema de dosificación de polvo que puede utilizarse es el dosificador vibratorio. Los alimentadores vibratorios utilizan motores de vibración y la estructura se apoya en muelles que permiten que la unidad vibre. La cubeta tiene una pendiente mínima que permite a la unidad desplazar el material hacia el final de la bandeja para alimentar el proceso aguas abajo.
La velocidad de avance puede controlarse aumentando o disminuyendo la amplitud y la frecuencia de las vibraciones. Este tipo de alimentador de polvo ayuda a mantener la integridad del producto o a evitar un desgaste innecesario en el caso de materiales abrasivos. El alimentador de tornillo se acciona para el último 5% del objetivo de llenado del súper saco. Mediante el uso de un alimentador fraccionado como el descrito anteriormente, los sistemas de llenado automatizados pueden llenar bolsas grandes de forma rápida y eficiente con precisión.
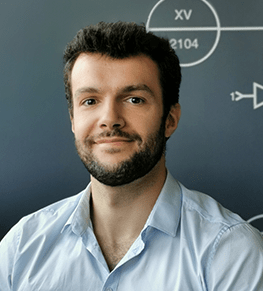
¿Busca una estación de llenado de súper sacos? Estoy a su disposición
para asesorarle y acompañarle en su estudio.
Paul, experto en polvo
3. Contención y control del polvo
Uno de los equipos más esenciales para cualquier instalación de producción industrial es la recogida y filtración de polvo. También es esencial que todo el equipo de manipulación esté diseñado para funcionar de forma estanca al polvo y contener los polvos que se manipulan. Los riesgos son importantes: toxicidad del material y exposición de los operarios, accidentes por resbalones y caídas debido a la presencia de polvo en el suelo, fallos mecánicos del equipo, relación de la mezcla aire/polvo que provoque una explosión, etc.
Hay varios tipos de colectores de polvo a considerar:
- Sistemas centralizados de recogida de polvo para todos los equipos de producción. Entre ellos se encuentran los filtros de bolsa de tela, los separadores inerciales (como los ciclones mecánicos), los filtros húmedos, los colectores de cartucho y los precipitadores electrostáticos
- Unidades de filtro de polvo integradas específicas para cada equipo: por ejemplo, filtro de polvo integrado en la parte superior de una estación de vaciado de bolsas
- filtros de desgasificación
- Campanas extractoras
- Anillos de recogida de polvo (anillos Pouyes): en la parte superior de un tanque de almacenamiento, por ejemplo, donde los operadores alimentan manualmente las bolsas de polvo.
Las unidades de recogida de polvo suelen estar equipadas con cartuchos filtrantes de montaje lateral o superior. Estos filtros se conectan a un tanque de aire comprimido externo que se ajusta a un ciclo temporizado. A medida que el polvo pasa por el filtro, se envía un chorro de aire intermitente desde el lado opuesto para limpiar la acumulación excesiva de polvo. Este sistema de limpieza por chorro de pulso inverso tiene dos funciones:
1. Evita que los filtros se obstruyan sin necesidad de mantenimiento
2. Ayuda a recuperar el producto que se ha escapado en los filtros.
Cuando se llenan big bags, es importante que la conexión entre el cabezal de llenado y el vertedero de súper sacos sea segura y hermética al polvo.
El método más común es utilizar un sello de hinchamiento en la cabeza de llenado. El operario posiciona la tolva del súper saco alrededor del sello de elastómero. Se introduce aire a presión en la junta, lo que hace que se hinche y que la canaleta quede firmemente sujeta.
El cabezal de llenado también puede tener una doble camisa (un tubo interior rodeado por un tubo exterior). El canal interior permite el paso del polvo y el llenado del súper saco. El canal exterior permite que el aire y el polvo muy ligero salgan a través de una pieza de conexión. Esta espiga puede estar equipada con una manga filtrante o una manguera que se conecta a un colector de polvo central. En las unidades de producción que procesan materiales especialmente tóxicos, como los polvos de litio en la industria de fabricación de baterías, toda la instalación puede instalarse en un recinto diseñado para aspirar un vacío atmosférico constante a un sistema externo de recogida de polvo.
4. Mesa vibratoria de densificación y células de carga
Uno de los problemas más comunes a la hora de transportar y almacenar súper sacos llenos de polvos y materiales granulares es el de la falta de estabilidad. Esto se debe a que las partículas de polvo se "airean" demasiado durante el proceso de llenado.
Cuando el material se asienta por gravedad por sí mismo, puede producirse la separación de partículas. Como resultado, las partículas finas caen al fondo y las partículas más grandes permanecen en la parte superior.
Esto puede hacer que el súper saco se hunda y se incline hacia un lado, lo que provoca una gran inestabilidad al moverlo o apilarlo durante el almacenamiento.
Las mesas vibratorias de densificación son un componente necesario de cualquier línea de producción de llenado de súper sacos semiautomática o totalmente automatizada.
A medida que la bolsa se llena de material a granel, la mesa de densificación vibra de forma intermitente. Esta vibración permite que salgan pequeñas bolsas de aire entre las partículas, con lo que éstas se unen. Esto limita la segregación de partículas y hace que el súper saco sea más rígido y, por tanto, más fácil de transportar y almacenar.
Además, la instalación de un transductor de fuerza en esta mesa vibratoria convierte una fuerza como la tensión, la compresión, la presión o el par motor en una señal eléctrica que puede medirse y normalizarse. A medida que la fuerza aplicada a la célula de carga aumenta, la señal eléctrica cambia en consecuencia.
Las celdas de carga o células de carga están conectadas a un controlador lógico programable (PLC) que lee la cantidad de peso que entra en un big bag durante la secuencia de llenado.
Se programa un peso objetivo en el panel de control. Cuando las células de carga indican que el súper saco está casi completamente lleno, el PLC envía una señal a la unidad de dosificación de polvo (alimentador de tornillo, válvula rotativa) para reducir la velocidad y verter el último 5% del peso objetivo.
Cuando se alcanza el peso objetivo, las células de carga envían una señal al PLC que indica a la válvula que se cierre y deje de llenar. Mediante el uso de células de carga, podemos automatizar la secuencia de llenado sin la intervención de un operario y obtener así un peso de llenado muy preciso.
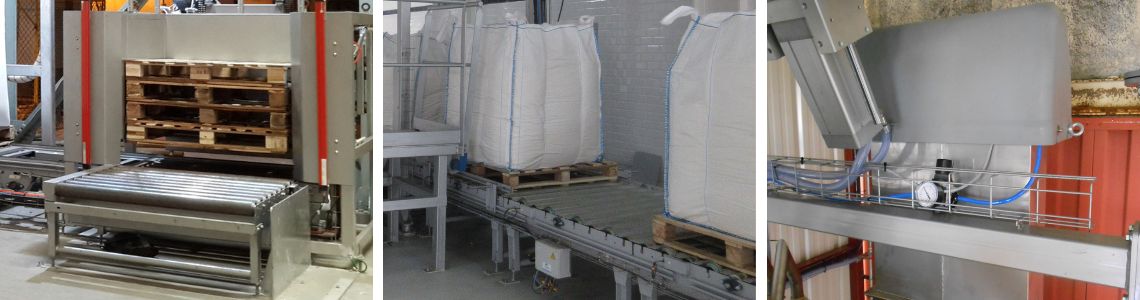
5. Desapilador de palets y transportador mecánico de rodillos
Los dos últimos componentes esenciales para automatizar su línea de llenado de FIBC son los desapiladores de palets y los transportadores de rodillos mecánicos.
Los desapiladores de palés utilizan brazos indexados robóticos conectados a cilindros neumáticos que pueden levantar, bajar y colocar un palé en una estación de llenado.
Pueden albergar hasta 20 palés a la vez. La máquina alimenta un palé cada 35 segundos y puede diseñarse para adaptarse a diferentes tamaños de palés. Cada vez que se termina de llenar un súper saco, el PLC puede indicar al desapilador de palés que coloque el siguiente en el transportador mecánico de rodillos.
Los transportadores mecánicos de rodillos tienen varias funciones diferentes, pero en este caso se utilizan principalmente para transferir los palés a la estación de llenado y, a continuación, descargar el súper saco lleno a una zona de almacenamiento intermedio. A continuación, un operario recoge el súper saco lleno con una carretilla elevadora y lo transporta a la zona de almacenamiento final. Todos los parámetros y secuencias son controlados por el PLC, lo que elimina cualquier trabajo manual. Los rodillos del transportador están espaciados uniformemente y son accionados por un motor de engranajes situado en el lateral, o por gravedad con un ángulo mínimo de inclinación. Los transportadores de rodillos por gravedad tienen rodillos de control de velocidad que se utilizan para controlar la velocidad de la carga que se transporta, como un big bag en su palé en nuestro caso. Independientemente del tipo de transportador, funcionan en secuencia para proporcionar un flujo constante de súper sacos hacia y desde la estación de llenado.
Con estos dispositivos, las operaciones de llenado de súper sacos reducen al mínimo el número de operarios en un mismo puesto de trabajo.