Carga de big bags de carbonato de sodio a gran velocidad
Polvo procesado: ceniza de sosa natural
Nuestro cliente, situado en el norte de California, es una empresa de distribución y logística para la exportación de ceniza de sosa natural. El proyecto consiste en la construcción de una instalación de envasado de última generación para la distribución al por mayor y la exportación de ceniza de sosa natural en big bags.
Requisitos del proyecto:
- Un sistema de llenado de big bags de alto rendimiento que puede funcionar a diario con una intervención mínima del operario
- El objetivo de llenado de big bags es de 120 big bags/hora con dos tamaños de saco diferentes: 1 y 1,25 toneladas métricas.
- El sistema de carga de big bags debe funcionar de forma coordinada con el sistema de entrega de vagones y la tolva pulmón de 150 toneladas (infraestructura existente del cliente).
El objetivo general de las líneas de llenado de big bags es automatizar al máximo el proceso, incluyendo la conformación de los big bags, el llenado, el pesaje, la extracción, el sellado y la transferencia a una zona intermedia.
Soluciones implementadas por Palamatic Process :
- Transportadores de tornillo
- Tolvas tampón pesadas
- Estaciones FlowMatic®06 - Sistemas automáticos de llenado de big bags
- Controles y automatización
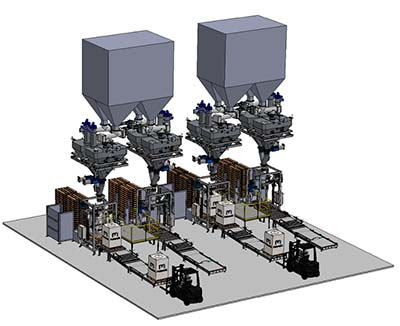
1. Transportadores de tornillo
Al principio de la planta se encuentran los transportadores de tornillo (o tornillos tubulares) necesarios para ayudar a extraer y transferir la ceniza de sosa desde la tolva de almacenamiento primario situada encima de la planta.
Se eligieron los transportadores de tornillo tubular en lugar de las válvulas rotativas estándar para reducir la altura total de la estructura, así como para lograr una mayor precisión en la dosificación del polvo en las tolvas de almacenamiento intermedio situadas debajo. Los transportadores de tornillo pueden controlarse automáticamente con un VFD (accionamiento de frecuencia variable) y permitiendo que otros componentes, como las células de carga y los sensores de nivel, se comuniquen con el equipo de transporte de polvo a través de un PLC.
Para este proyecto, los transportadores de tornillo tienen aproximadamente 30 cm de diámetro y 1,2 m de longitud. La estructura tubular y el paso de los tornillos están ligeramente inclinados, lo que permite ahorrar espacio y altura entre el depósito de acumulación (arriba) y las tolvas pulmón (abajo). El material se transporta a un ritmo de 39 kg por hora.
2. Tolvas tampón pesadas
Para lograr un ritmo de llenado de 120 big bags por hora, la solución es instalar 4 líneas de llenado con 2 tolvas de almacenamiento intermedio para cada cabezal de llenado. Con este método, una tolva se llena de ceniza de sosa mientras la otra llena la bolsa grande de abajo. Al trabajar con tolvas de material a granel en tándem, la operación de llenado del big bag de abajo puede funcionar en tiempo secuencial sin interrupción. Con este diseño, el rendimiento se duplica en cada línea del sistema de llenado.
La capacidad de almacenamiento de cada tolva de almacenamiento es de 1500 litros. Las salidas de la tolva están equipadas con válvulas de compuerta neumáticas para el control del flujo de material a través de un PLC. Otros componentes integrados son los sensores de nivel alto y bajo, las células de carga y los cañones de aire. Las sondas de nivel y las células de carga proporcionan los dispositivos de medición necesarios para permitir un control totalmente automatizado y sin operarios de las operaciones de selección y llenado de tolvas.
Toda la planta se encuentra al aire libre, pero hay cierta protección contra la exposición a la intemperie con una estructura de techo cubierta. Sin embargo, la ceniza de sosa es higroscópica y, si se almacena durante demasiado tiempo, puede presentar problemas de flujo, como la formación de puentes. Por este motivo, las tolvas pulmón también están equipadas con cañones de aire y vibradores para garantizar que el producto fluya si se compacta o se expone a altos niveles de humedad.
Para ayudar a equilibrar el volumen de aire y material durante la secuencia de llenado de big bags, se incorpora un filtro de polvo en la parte superior de las tolvas de almacenamiento. De este modo, el polvo y las partículas finas pueden retirarse y desplazarse con seguridad a medida que el material se descarga en el big bag.
3. FlowMatic®06 - Sistema automatizado de llenado de big bags
Palamatic Process ha diseñado un sistema de carga de big bags que ofrece una completa automatización de todas las secuencias operativas con una mínima intervención del operario. El modelo FlowMatic®06 ofrece una solución llave en mano para todas las etapas de tamponamiento, alimentación, dosificación, pesaje, llenado, densificación y depósito.
Para la producción total requerida de 120 big bags por hora (es decir, 30 big bags por hora en cada estación de llenado), el sistema ha sido equipado con todas las funciones necesarias, como tolvas de pesaje predosificadas, un sello de contención inflable, ganchos automáticos para las correas de los big bags, un cabezal de fijación de big bags giratorio, una plataforma regulable en altura mediante un cilindro neumático, un ventilador para dar forma al big bag, una báscula comercial para la reventa certificada de los envases rellenos, una mesa vibratoria para densificar el refresco y estabilizar el big bag, un desapilador de paletas y un transportador de rodillos motorizado para transferir los big bags rellenos
El ciclo de funcionamiento es el siguiente:
- El desapilador de palets introduce un palet en el transportador de rodillos motorizado.
- El operario engancha el big bag a los ganchos automáticos por las correas y conecta la boquilla de llenado a la junta hinchable.
- Los ganchos se bloquean y el sello se infla, asegurando la bolsa grande en su lugar.
- El cilindro neumático levanta el big bag de la paleta para crear una tensión que permita un llenado y un moldeado óptimos.
- Un ventilador de preinflado infla la bolsa para evitar las arrugas y mejorar el llenado de la bolsa grande
- La válvula de derivación del ventilador pasa del modo de inflado al de ventilación (equilibrando el volumen de material y de aire).
- La válvula neumática se abre y comienza el llenado del big bag.
- El cilindro neumático hace descender suavemente el big bag sobre las células de carga inferiores.
- La mesa vibratoria de densificación agita la bolsa para ayudar a estabilizarla y optimizar el llenado.
- Las células de carga indican a la válvula de compuerta cuando se alcanza el peso objetivo y cierran la válvula de polvo.
- La segunda vibración tiene lugar para terminar de empaquetar el material.
- El sello inflable se desinfla y los ganchos automáticos liberan la bolsa grande.
- El transportador de rodillos motorizado transfiere el big bag a una estación de sellado para acoplar la boquilla del big bag.
- El big bag se transporta a una zona de almacenamiento temporal para su retirada por un operador de carretilla elevadora.
Nuestro equipo realizó un estudio de tiempos sobre todas las secuencias operativas (línea de tiempo) y determinó que entre las tareas del operario y los controles del sistema automatizado, cada big bag tenía un ciclo total de llenado y transferencia de 2 minutos cada uno.
Centrarse en cada componente funcional de la estación de envasado de big bags:
El cabezal de llenado tiene una junta de elastómero que puede inflarse mediante el suministro de aire comprimido de la planta. Contiene un sensor de límite de presión para evitar que se dañe la junta. Esto proporciona una conexión segura y hermética al polvo con la boca de llenado del big bag. Garantiza que la boquilla no se deslice durante la secuencia de llenado de polvo.
Los ganchos automáticos tienen un riel motorizado integrado que permite que los ganchos traseros se muevan hacia adelante para mejorar la ergonomía del operador. Una vez que el operario ha asegurado las correas del big bag a los ganchos, éstos se deslizan hacia atrás y bloquean las correas en su lugar.
El cilindro neumático tiene un sistema de tensión por resorte. Antes del llenado, el big bag se levanta de su plataforma para permitir que el fondo y los lados del big bag mantengan una forma óptima. A medida que el material llena el big bag, el muelle permite que el big bag descienda gradualmente hasta el palé.
El ventilador de inflado ayuda a dar forma a la bolsa grande para evitar que se arrugue el tejido. De este modo, no hay bolsas de aire muerto después de que el material haya llenado el FIBC. Una vez inflado, una válvula de derivación cambia a una línea de recogida de polvo para permitir que el aire y las partículas finas salgan a través del filtro de polvo de las tolvas de almacenamiento intermedio pesadas. Los filtros están conectados a un tanque de aire comprimido que envía un chorro de aire a presión a través del cartucho del filtro para limpiarlo y evitar la acumulación de material. El sistema de limpieza por chorro de pulso inverso funciona en una secuencia temporizada y recupera el polvo que pueda perderse a través de los filtros.
La mesa de densificación vibratoria utiliza dos motores vibratorios en lados opuestos de un marco metálico ranurado. La mesa es desmontable para permitir el posicionamiento y la transferencia de la paleta al transportador de rodillos. Las ranuras metálicas encajan entre el transportador de rodillos para entrar en contacto con la paleta. A medida que se llena el big bag y se baja a la paleta, la mesa vibra, permitiendo que salgan pequeñas bolsas de aire entre las partículas de polvo, lo que densifica el material. Esto garantiza que los límites de capacidad del big bag se llenen de forma óptima y que se estabilice para que no se doble, evitando así accidentes y derrames de material.
La línea de transportadores de rodillos transfiere los palés vacíos al cabezal de llenado de big bags y el big bag a su palé una vez lleno. La línea comienza con el desapilador de palés, que ha sido diseñado para acomodar dos tamaños de palés diferentes. La capacidad total del desapilador se ha diseñado para albergar hasta 20 palés a la vez. Cada línea está equipada con dos cargadores de palés, para una capacidad total de almacenamiento de 40 palés, lo que permite una hora de funcionamiento sin recargar el equipo. Dos carros verticales de indexación montados sobre guías y accionados por cilindros neumáticos proporcionan el movimiento de subida y bajada y las tres posiciones necesarias para la elevación y descarga de palets. Una estructura de raíles guía empuja las paletas fuera del desapilador y hacia el transportador de rodillos. Además, este sistema de alimentación de palets viene con las siguientes características: 2 sensores inductivos para las posiciones de horquilla delantera y trasera, 3 sensores inductivos para las posiciones de horquilla baja, media y alta y 1 sensor fotoelectrónico para indicar la presencia de un palet en el transportador de rodillos.
A continuación, el transportador de rodillos motorizado traslada la paleta vacía a la estación de llenado. La capacidad de carga de los transportadores mecanizados es de 1,2 toneladas por metro y su longitud total es de 1,35 metros. Una vez que el big bag está lleno, el transportador empuja el big bag hacia el palé y hacia un transportador de rodillos por gravedad. Al utilizar transportadores de rodillos por gravedad, la planta puede ahorrar energía. Al final del transportador de rodillos por gravedad hay rodillos reguladores que ayudan a reducir la velocidad del big bag y un separador de palés que permite separar cada palé para que lo retire un operario de la carretilla.
4. Controles y automatización
El controlador fue diseñado por nuestro departamento interno de automatización y electricidad. El armario de control está fabricado en acero templado con revestimiento epoxi y cuenta con una pantalla táctil de 7". El PLC está formado por componentes Allen Bradley, Micrologix 850 con conexión Ethernet. En este sistema se instaló un tablero de control PLC principal y 4 cajas de control local. Palamatic Process también ofrece capacidades de diagnóstico remoto mediante la integración de una caja de mantenimiento remoto ethernet. Esto permite a nuestros equipos realizar diagnósticos remotos y solucionar cualquier error o mal funcionamiento del sistema en tiempo real. Palamatic Process diseña, monta y programa todos los paneles de control en la empresa. Nuestro equipo de ingenieros de automatización incluye una fácil entrada de materias primas, trazabilidad de los lotes, identificación de los operarios y una dosificación fiable. El PLC gestiona y controla el llenado de big bags, la dosificación por pérdida de peso, el transporte, el desempolvado, la alimentación y la selección de tolvas. Nuestros técnicos también están disponibles para la puesta en marcha in situ y la asistencia a la formación.
Póngase en contacto con uno de nuestros expertos hoy mismo para que le ayude con las soluciones de manipulación de materiales que necesita y para solicitar un presupuesto.