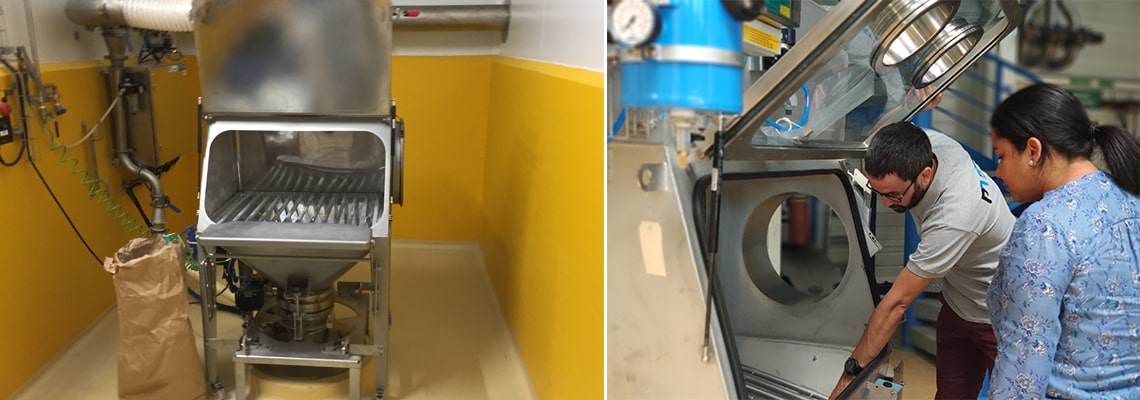
Los sólidos secos a granel se almacenan y envían utilizando una variedad de envases y contenedores. Una de las prácticas más habituales es utilizar sacos de 50-75 kg que contienen diversos materiales a granel y polvos. A menudo fabricados en polietileno o papel, son fáciles de apilar y desapilar en palés para el transporte a granel. Sin embargo, estas bolsas de polvo pueden ser más intensivas en mano de obra, ya que a menudo requieren que un operador levante, corte y vierta manualmente el material en un proceso de producción. Varias industrias utilizan este método de suministro de polvo, como las industrias química, alimentaria y de minerales, por nombrar sólo algunas. Las estaciones de descarga de bolsas están presentes en muchas instalaciones de producción de polvo seco. Crean un lugar para apoyar la bolsa de manera que el operario pueda cortar y verter el material en el proceso posterior.
Las estaciones de descarga de bolsas pueden ser de construcción muy simple, ofreciendo una rejilla en la que se apoya la bolsa, una puerta con bisagras para el acceso y una tolva con una brida para ayudar a entregar el polvo a la producción. Sin embargo, existen muchas opciones y características para satisfacer las demandas específicas de ciertas líneas de producción. Por eso, antes de comprar una estación de descarga de bolsas, debería hacerse las siguientes preguntas.
1. ¿Cuál es el riesgo de exposición para el operador y qué nivel de contención debe proporcionar?
Algunos polvos pueden ser potencialmente peligrosos para el sistema respiratorio del operario o contener carcinógenos tóxicos. Su proveedor de equipos debe ser capaz de ofrecer soluciones que salvaguarden la salud de sus trabajadores.
Los diseños de las guanteras pueden ayudar a mantener una barrera física entre la operación de descarga de polvo y el operador. Este tipo de instalación suele utilizar un alimentador manual de rodillos laterales con una puerta de solapa para facilitar la colocación de los sacos dentro de la estación. Una vez dentro, el operario puede utilizar guantes de látex o nitrilo integrados en la ventana frontal transparente. Por lo tanto, el operario está totalmente protegido de la exposición mientras tenga esta barrera para cortar y verter el polvo.
Muchos polvos pueden tener una densidad aparente muy baja, lo que significa que las partículas pueden esparcirse por el aire mucho más fácilmente que las que tienen una densidad aparente más alta. Las bandejas de ensacado a menudo pueden proporcionar una conexión a una planta de ensacado existente o un sistema completo de filtración de polvo por chorro pulsante integrado en la propia unidad. La incorporación de un filtro de polvo es un elemento clave en el diseño de una estación de descarga de sacos de polvo para garantizar su estanqueidad durante el funcionamiento.
¿Qué se hace con el saco vacío una vez que el polvo se ha descargado en el proceso de producción? Una práctica habitual en muchas plantas de producción es simplemente tirar los sacos abiertos a un contenedor y aplastarlos físicamente cuando los residuos de sacos empiezan a acumularse y a ocupar espacio.
Los compactadores de sacos proporcionan un método seguro y contenido de eliminación de residuos de sacos vacíos. Los compactadores pueden integrarse directamente en el lateral o en la parte trasera de una estación de descarga de bolsas o ofrecerse como solución independiente.
2. ¿Su material contiene grumos o tiene malas propiedades de flujo?
Los sacos que han sido transportados durante largas distancias suelen estar comprimidos cuando llegan a su destino. El polvo también puede haber estado expuesto a la humedad. En este caso, los polvos de los sacos suelen formar aglomerados blandos y/o duros que hay que descomponer antes de introducirlos en su proceso de producción.
Una opción a tener en cuenta es la criba vibratoria (también conocida como tamiz vibratorio o criba plana), que consiste en una criba de malla circular y un motor vibratorio externo. El motor puede ajustarse para intensificar la vibración y asegurar un buen flujo de su polvo a través de la malla de la criba. Pueden diseñarse para un rápido montaje y desmontaje para su limpieza en procesos de producción sanitarios e higiénicos.
Otra opción común es incorporar un rompe grumos directamente debajo de la salida de la bandeja de ensacado. Las trituradoras (también llamadas rompedoras de grumos o granuladoras) suelen estar diseñadas con un motor externo, una carcasa, dientes giratorios y una rejilla fija para la clasificación básica de los aglomerados. Los medios de molienda giratorios golpean los trozos de polvo sólido contra la rejilla fija, permitiendo que los aglomerados se rompan y vuelvan a su estado granular natural.
Si su material en polvo es pegajoso, tiene puentes o simplemente tiene malas propiedades de flujo en general, se pueden instalar ayudas de flujo en la tolva de descarga de la estación de descarga de sacos. Hay muchos tipos de ayudas al flujo, pero los más conocidos son los vibradores de turbina de aire, los vibradores de rodillo de aire, los aireadores de tolva y los dispositivos antipuente. En la mayoría de las aplicaciones, se utilizan ayudas de flujo vibratorias montadas externamente para agitar el producto de la superficie de la tolva y facilitar la descarga de los sólidos a granel en el proceso posterior.
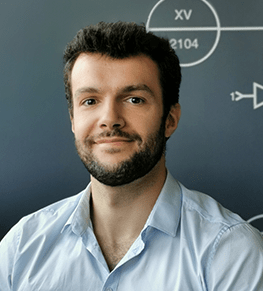
¿Tienes un proyecto? Estoy a su disposición
para asesorarle y acompañarte en tu estudio.
Paul, polvo experto
3. ¿Cuáles son sus objetivos de producción?
¿Cuántos sacos de 50 kg necesita descargar por hora (o minuto) de producción? ¿Qué nivel de automatización necesita para su proceso de producción? ¿Y si necesita descargar sus materiales a un ritmo de 6 sacos por minuto?
Un operario con un solo estante de descarga de sacos no podrá alcanzar ese ritmo de producción. Muchas plantas de producción pueden optar por estaciones de descarga de seis sacos con seis operadores para estas estaciones.
Existen otras alternativas como las ensacadoras semiautomáticas (Ergotip®, SAS) o totalmente automáticas (Minislit®, Varislit®, Rotaslit®). Los proveedores de equipos pueden ofrecer diferentes grados de automatización para ayudar a un operario a descargar sacos de polvo a granel.
Algunas bandejas semiautomáticas de descarga de bolsas pueden ofrecer un dispositivo de sujeción para mantener el saco en su sitio mientras una cuchilla neumática perfora el fondo de la bolsa. Los brazos plegables de accionamiento neumático pueden entonces doblar la bolsa por la mitad para facilitar la descarga del contenido del saco.
Las versiones totalmente automatizadas pueden incluir una cinta transportadora o un transportador de rodillos para introducir los sacos en una cámara de corte. Una vez que la bolsa está en la cámara, los sensores detectan la bolsa y activan un dispositivo de corte (por ejemplo, una sierra de cinta) para abrir parcialmente la bolsa. La bolsa se voltea, derramando su contenido, y luego se introduce en un compactador de bolsas integrado para la eliminación automática de los residuos, la contención y la compactación para la reducción del volumen. Los brazos despaletizadores robóticos también pueden utilizarse para ayudar a cargar los sacos de polvo en la cinta transportadora motorizada, para una automatización total sin intervención del operario.
Dependiendo del tipo de polvo y de bolsa, muchos sistemas automáticos de apertura de sacos pueden alcanzar tasas de 6 a 8 sacos por minuto por estación.
4. ¿Qué otras opciones deberían considerarse?
El equipo de elevación de sacos de vacío es otro dispositivo de apoyo que ayudará a los operarios a reducir el esfuerzo repetitivo de levantar pesados sacos de polvo. También conocidos como manipuladores de sacos, funcionan según el principio de succión que mantiene el saco en su lugar en el pie de sellado del equipo. Aumentando o disminuyendo la cantidad de succión, el operario puede subir y bajar el saco con un esfuerzo mínimo. Los elevadores de vacío suelen constar de una bomba de vacío, mangueras ajustables, asas de elevación y descenso, y un brazo montado en el suelo o en la pared que puede girar sobre su eje. Además, estos elevadores por vacío suelen adaptarse a diferentes tipos de contenedores cambiando rápidamente la bota de aspiración (es decir, bidones, cubos, cajas, balas de goma, palés, etc.).
¿Qué pasa si necesita transferir el material a granel a una tolva o a un equipo de mezcla posterior? Los transportadores de tornillo se utilizan habitualmente a la salida del descargador de sacos para trasladar el material descargado a la siguiente etapa de su proceso. También se pueden incorporar válvulas rotativas y sistemas de transporte neumático en el extremo de salida de la estación de descarga de sacos.
¿Y si su proceso requiere la descarga de sacos a granel para los ingredientes primarios (como el azúcar y la sal) y sacos de 50 kg para los ingredientes secundarios? Los proveedores de equipos pueden integrar una estación combinada de descarga de sacos y bolsas en una sola unidad. El saco a granel puede estar suspendido sobre la bandeja de soporte en la que descansa mientras un operario puede acceder a la caja de desencuadernación que también actúa como bandeja de descarga de sacos. Se trata de dos métodos de descarga en un flujo de productos.
Póngase en contacto con uno de nuestros expertos hoy mismo para obtener ayuda sobre las soluciones de manipulación de sacos que necesita y/o para solicitar un presupuesto.